Dopo i robot che costruiscono altri robot, i ricercatori del Massachusetts Institute of Technology hanno realizzato un sistema automatizzato che progetta e stampa in 3D complesse parti robotiche, ossia gli attuatori. In estrema sintesi, il nuovo sistema fa automaticamente ciò che è virtualmente impossibile da fare per gli umani, a mano.
L’idea è talmente rivoluzionari da essersi meritata la pubblicazione sulla rivista scientifica Science Advances, e descrive come un sistema del tutto autonomo possa fabbricare attuatori, ossia quei componenti dei robot che ne controllano meccanicamente i movimenti in risposta a segnali elettrici, un po’ come i muscoli del corpo umano.
Costruirli a mano è molto difficile perché bisogna testare milioni di combinazioni di parametri, materiali e movimenti, fino a trovare la misura corretta. Gli attuatori robotici ormai sono talmente complessi da dover essere ottimizzati per peso, efficienza, aspetto, flessibilità, consumo energetico e varie altre funzioni e parametri di prestazione, a seconda della situazione. Calcolare manualmente tutti questi parametri richiede molto tempo e lavoro. Con il metodo messo a punto al MIT, la maggior parte del processo viene automatizzato.
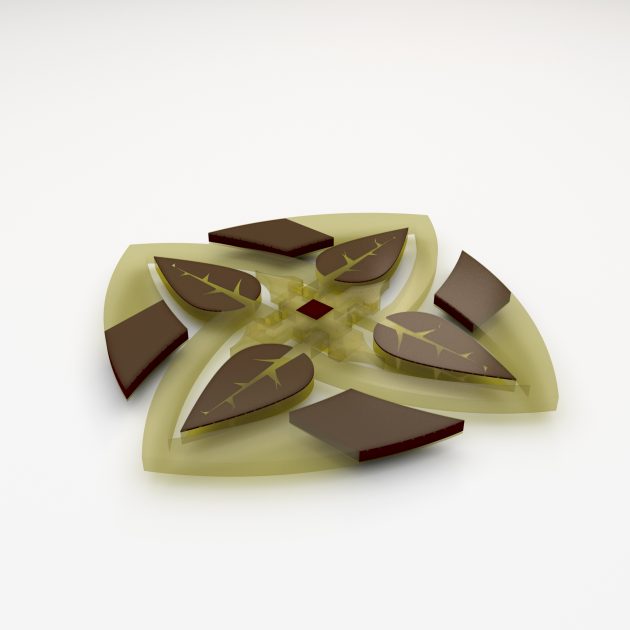
Gli attuatori sono realizzati combinando tre materiali diversi, ciascuno con un diverso colore (chiaro o scuro) e con una specifica proprietà (ad esempio la flessibilità o la magnetizzazione) che controlla l’angolo dell’attuatore in risposta a un segnale di controllo. Il tutto è controllato da un software, che scompone il design dell’attuatore in milioni di pixel tridimensionali, soprannominati “voxel”, che possono essere riempiti con qualsiasi materiale. A questo punto esegue milioni di simulazioni, riempiendo “voxel” differenti con materiali diversi fino a trovare quello ideale. Infine, si colloca nella posizione ottimale di ciascun materiale con cui è composto ciascun “voxel” e genera due immagini diverse per altrettante angolazioni. Una stampante 3D personalizzata costruisce l’attuatore facendo cadere il materiale giusto nel “voxel” giusto, strato per strato.
Il primo autore della ricerca, Subramanian Sundaram, spiega che l’obiettivo era “individuare automaticamente un design ottimale per qualsiasi problema, quindi utilizzare l’output del design ottimizzato per fabbricarlo. Per farlo selezioniamo i materiali di stampa, individuiamo il design ottimale, e realizziamo il prodotto finale in modo quasi del tutto automatizzato”.
Nella dimostrazione pratica, i nuovi strumenti hanno mostrato due differenti immagini in bianco e nero, solo modificando la propria angolazione: quando l’attuatore era piatto mostrava un ritratto di Vincent van Gogh, quand’era inclinato il famoso dipinto “L’urlo” di Edvard Munch. I ricercatori hanno anche stampato ninfee fluttuanti in 3D con petali dotati di matrici di attuatori, e cerniere che si piegano in risposta ai campi magnetici attraversati da fluidi conduttivi.
La stampante 3D ovviamente non è un comune modello, ma un prodotto realizzato appositamente dai ricercatori, che utilizza una tecnica chiamata “drop-on-demand“. Le taniche dei tre materiali sono collegate a testine di stampa con centinaia di ugelli controllabili individualmente. La stampante produce una goccia di dimensioni pari a 30 micron del materiale designato nella rispettiva posizione voxel. Una volta che la gocciolina atterra sul substrato, si solidifica. In questo modo, la stampante crea un oggetto, strato per strato.
A che cosa potrebbero servire attuatori ottimizzati per precisi aspetti e funzioni? Ad esempio per la biomimetica, la creazione di soluzioni tecnologiche ispirate da fenomeni biologici. Oppure come punto di partenza per progettare strutture più grandi, come le ali di aeroplani.